
Custom CNC Machining Services
Choose from 100+ materials, 60+ surface finishes. ISO 9001:2015, ISO 13485, ISO14001:2015, IATF 16949:2016
certified. Experience lead times as short as 1 day.
CNC Machining Services for Custom Parts
Our advanced milling centers and turning equipment deliver precision with tolerances as tight as 0.001 inches. Beyond standard machining, we provide value-added services like CNC routing, EDM machining, and precision grinding, perfect for designers and product developers seeking to actualize innovative ideas with top-quality custom components. Whether the project is straightforward or complex, our equipped machine shops are ready to take it on. We guarantee not only superior quality but also rapid delivery—custom simple machined parts are shipped within just 1 day. Get started.

Custom CNC Milling Services
CNC milling employs multi-axis operations, such as 3, 4, and 5-axis machining, to ensure precision and intricate geometries from blocks of metal or plastic, efficiently producing complex parts.
- Tolerances as tight as +/- 0.001 inches.
- Custom milled parts for prototyping and production.
- Quick turn milling services.
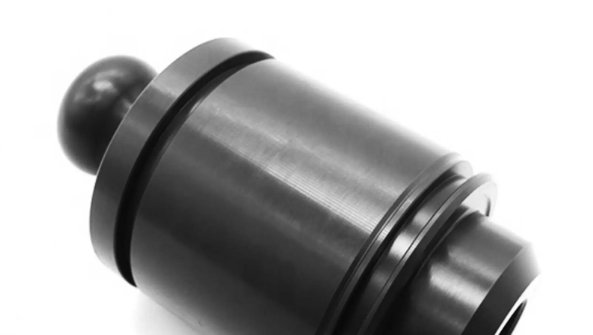
Custom CNC Turning Services
CNC turning uses CNC lathes and turning centers to shape metal rob stock, focusing primarily on cylindrical turned parts. Ensure components achieve consistent dimensions and smooth finishes.
- Achieves +/- 0.0005 inches precision.
- Custom turned parts for prototyping and production
- Quick turn turning services.
CNC Machining Materials
We work with a wide array of CNC materials, including both metals and plastics. Choose from aluminum, steel, brass, and more for your custom CNC machined parts.
![]() | Aluminum is lightweight yet strong, with excellent machinability and corrosion resistance. Ideal for aerospace and automotive parts. Alloys |
![]() | Copper is known for its superior electrical conductivity and thermal properties, making it perfect for electrical components and heat exchangers. Alloys |
![]() |
Brass is durable and has a low friction coefficient, which makes it suitable for fittings, tools, and musical instruments that require precision. Alloys Brass C27400 Brass C28000 Brass C36000 |
![]() |
Bronze is highly resistant to corrosion and metal fatigue, favored for bearings, bushings, and marine hardware.
Brass C36000Alloys Tin Bronze |
![]() |
Steel is an alloy with high tensile strength and durability, commonly used in construction and automotive industries for its robustness. Alloys Steel 1018, 1020, 1025, 1045, 1215, 4130, 4140, 4340, 5140, A36 Die steel Alloy steel Chisel tool steel Spring steel High speed steel Cold rolled steel Bearing steel SPCC |
![]() |
Stainless steel is renowned for its corrosion resistance, making it a prime choice for medical devices and food processing equipment. Alloys Stainless Steel SUS201 Stainless Steel SUS303 Stainless Steel SUS 304 Stainless Steel SUS316 Stainless Steel SUS316L Stainless Steel SUS420 Stainless Steel SUS430 Stainless Steel SUS431 Stainless Steel SUS440C Stainless Steel SUS630/17-4PH Stainless Steel AISI 304 |
![]() |
Magnesium is the lightest structural metal, offering high strength-to-weight ratios, perfect for automotive and aerospace applications where weight is critical.
Alloys Magnesium Alloy AZ31B Magnesium Alloy AZ91D |
![]() |
Titanium boasts the highest strength-to-density ratio among metals, highly resistant to corrosion and fatigue, ideal for aerospace, medical, and marine applications. Alloys Titanium Alloy TA1 Titanium Alloy TA2 Titanium Alloy TC4/Ti-6Al 4V |
Futai CNC Machining Solutions
PROTOTYPING
Rapid Prototyping
Accelerate product development with our rapid machining services. We offer fast turnaround times and specialize in quick production of high-quality prototypes and mold tooling, aiding your design verification process.
PRODUCTION
Low and High-Volume Production
Whether you need small batches or large-scale production, we can offer you both. With stringent tolerance controls and comprehensive capabilities, we adapt to your volume requirements without compromising on quality.
CNC Machining Surface Finishes
Achieve the perfect finish with our range of surface treatments. Whether you require anodizing, plating, or painting, we ensure your parts meet both aesthetic and functional specifications.
As Machined

As machined finish leaves thesurface straight from the CNCmachine, providing a cost-effective option with toolmarks.
Anodizing
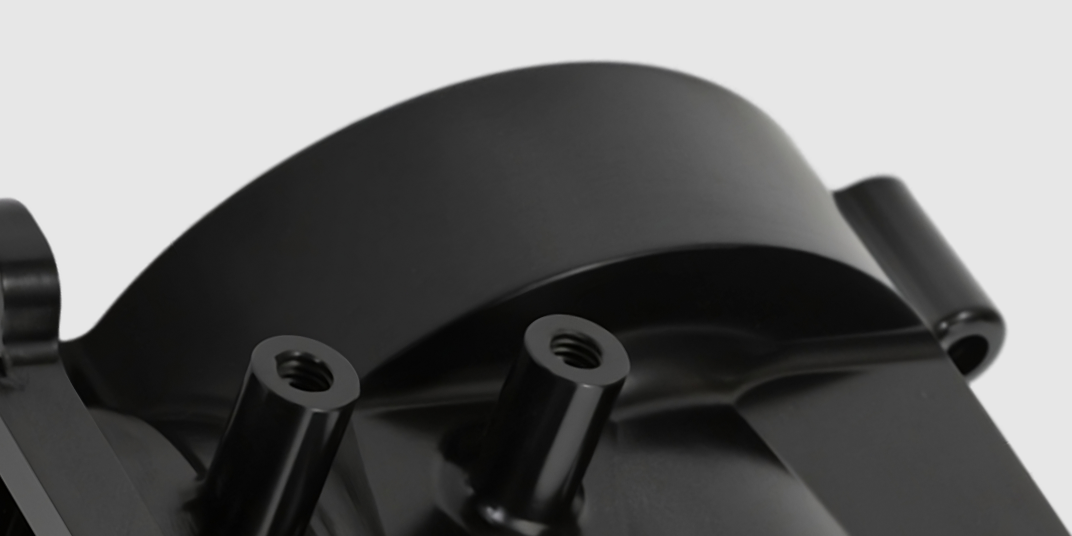
Anodizing increases corrosion resistance and wearproperties, while allowing forcolor dyeing, ideal for aluminumparts.
Polishing
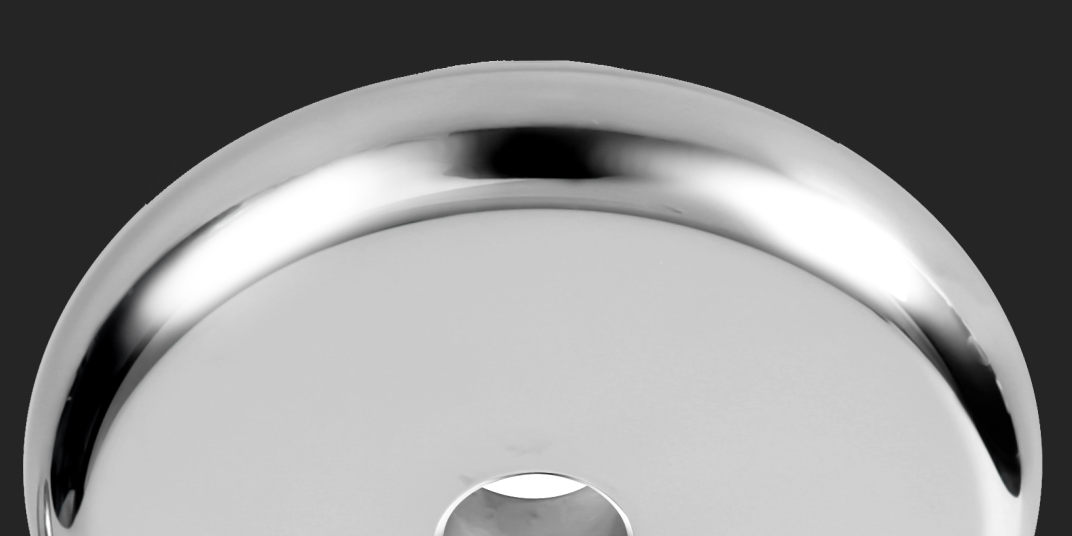
Polishing achieves a high glossfinish, reducing surfaceroughness and enhancing theaesthetic appeal of metals.
Sand Blasting
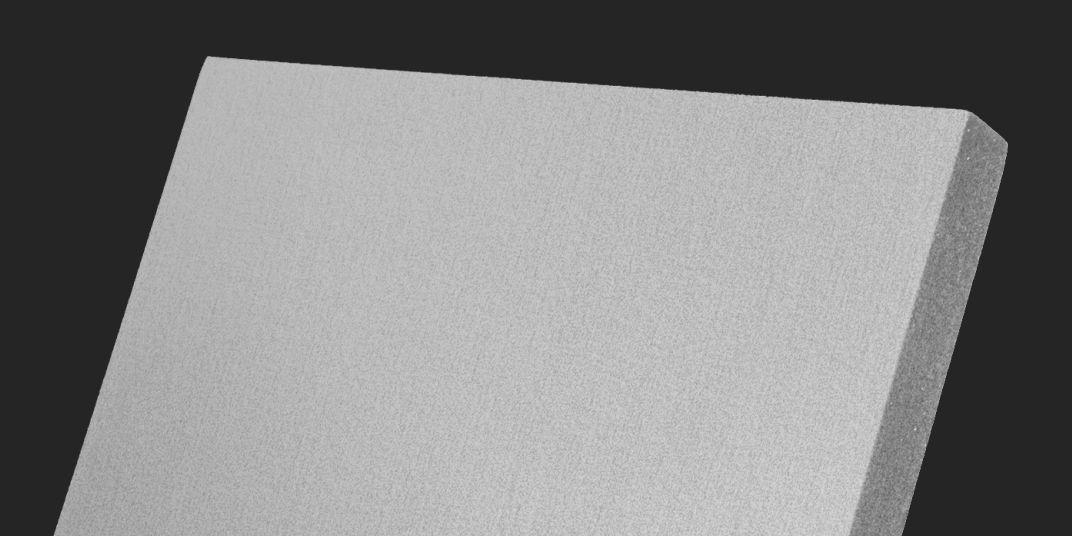
Sand blasting uses pressurizedsand or other media to cleanand texture the surface.creating a uniform,matte finish.
Tumbling

Tumbling smooths and polishes small parts by friction andabrasion in a barrel, offering aconsistent but slightly texturedfinish.
Electropolish
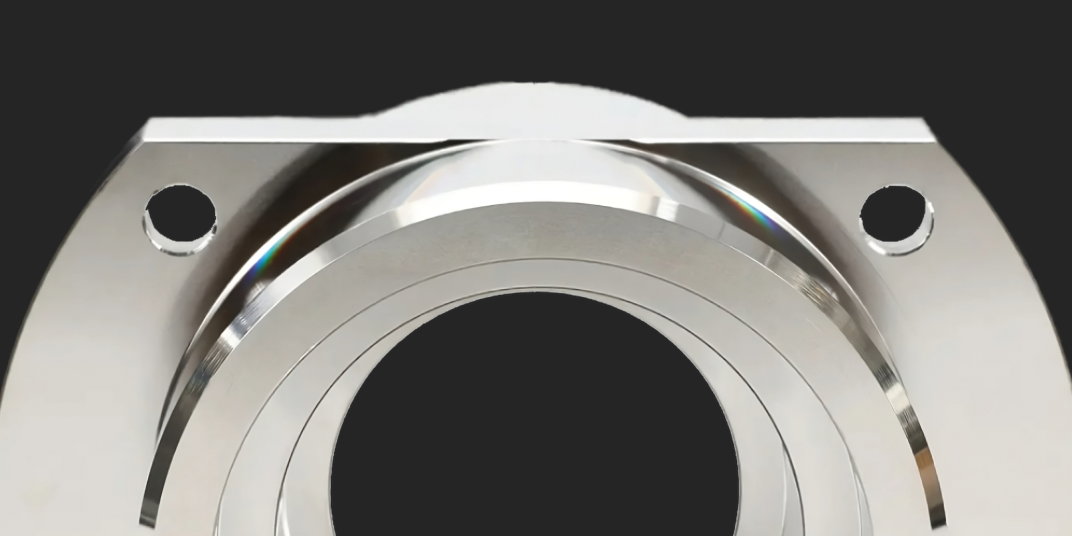
Electropolish is a chemicalprocess that smooths andbrightens surfaces whileimproving corrosion resistance.
Alodine

Alodine coating providescorrosion protection andimproves paint adhesion,mainly used on aluminumsurfaces.
Heat Treatment
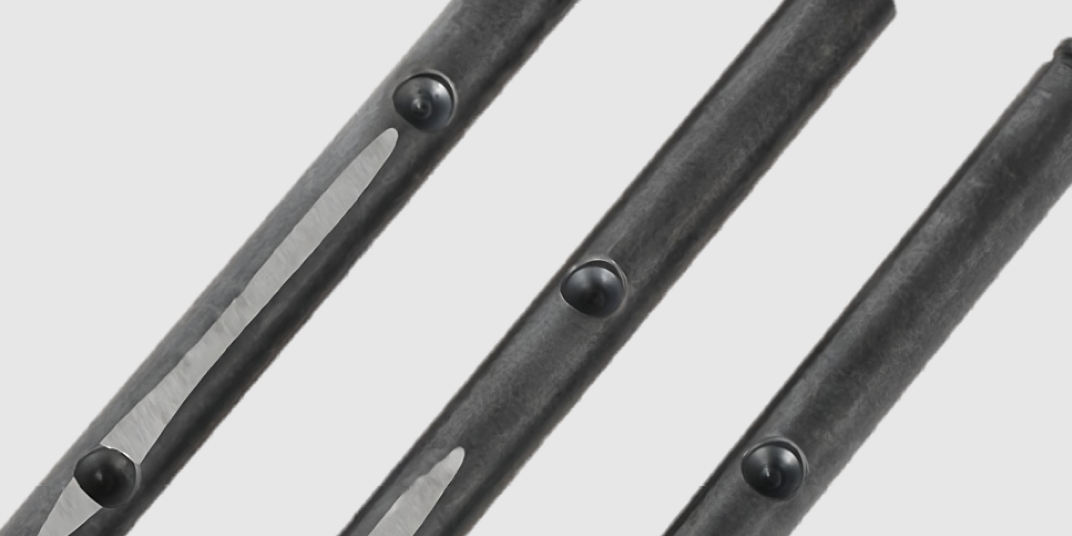
Heat treatment alters themechanical properties of metalto increase its hardness,strength, or ductility.
Brushed Finish

A brushed finish creates aunidirectional satin texture,reducing the visibility of marksand scratches on the surface.
Powder Coating
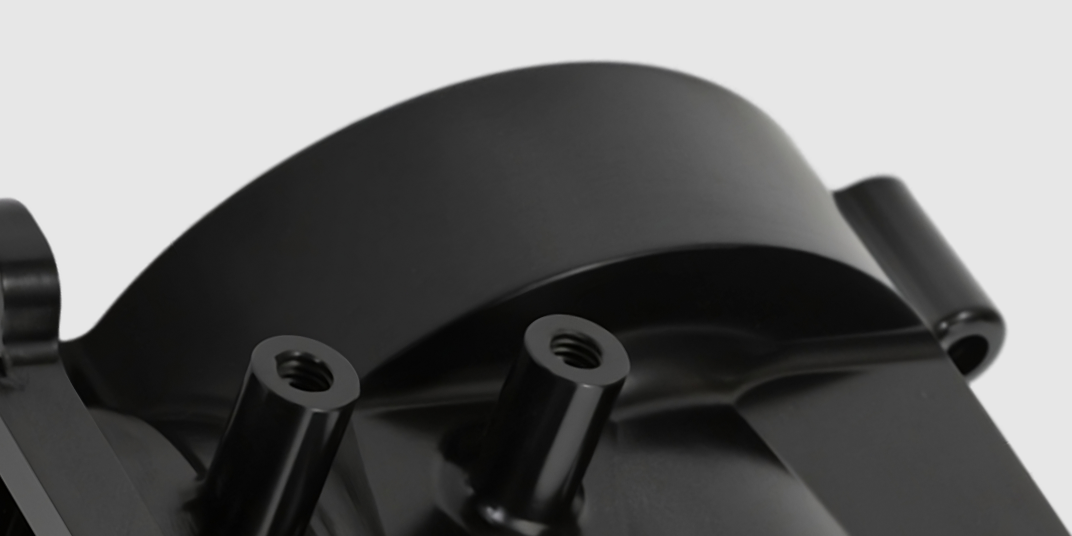
Powder coating applies a thick,wear-resistant layer withexcellent color and textureoptions, suitable for a variety ofsurfaces.
Electroplating

Electroplating bonds a thinmetal layer onto parts,improving wear resistance,corrosion resistance,andsurface conductivity.
Black Oxidize
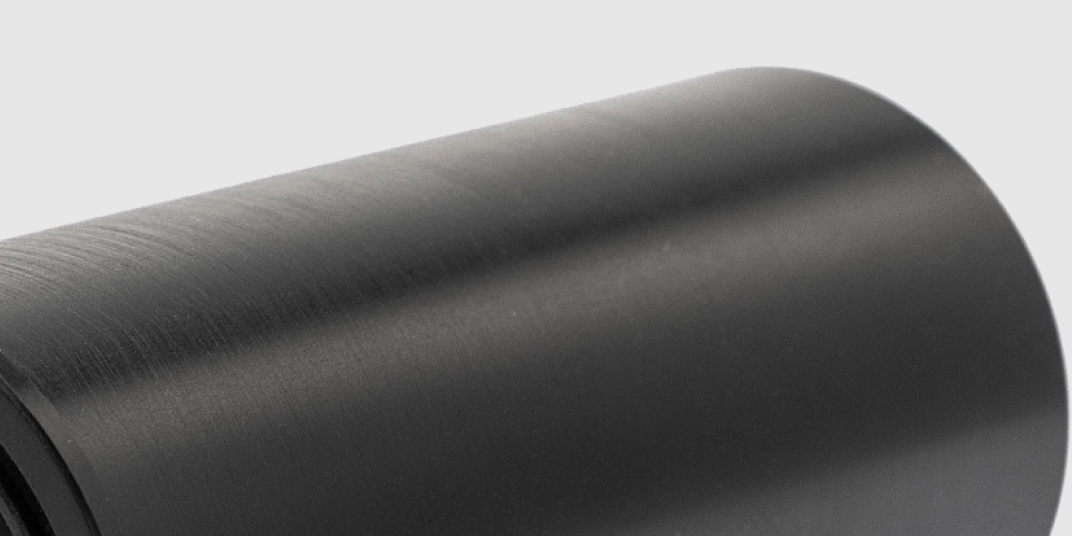
Black oxidize is a conversioncoating for ferrous metals thatimproves corrosion resistanceand minimizes light reflection.
Tolerances for CNC Machining
Our CNC machines operate with precision tolerances that meet industry standards, ensuring that every part is consistently accurate and fits perfectly with other components.
Description
Maximum Part Size
Typically up to 500 mm in diameter and 1500 mm in length, though larger sizes can be accommodated with specific equipment.
Minimum Part Size
As small as 1 mm in diameter, depending on the material and machining setup.
Design Guidelines for CNC Machining
Optimize your designs for manufacturability with our helpful guidelines. Our experts provide feedback on your custom machined part for the best results in CNC machining.
Recommended Size
Radii
Internal radii should be at least 1/3 of the cavity depth. Use larger radii whenever possible.
Threads and Tapped Holes
Diameter Φ 1.5-5 mm, depth: 3 times the diameter.
Diameter Φ 5 mm or larger, depth: 4-6 times the diameter.
RapidDirect can produce threads of any specification and size as required by the customer.
A Robust Network of CNC Machine Shops

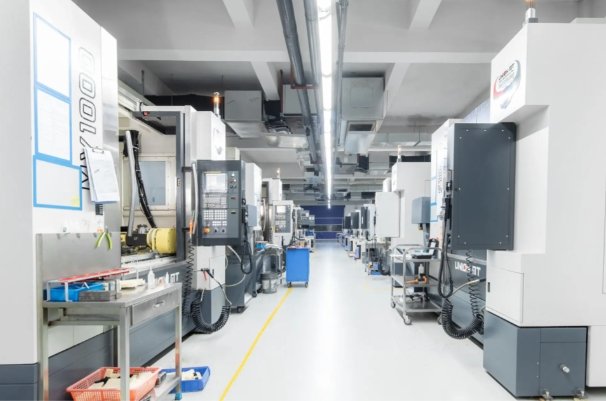
CNC machining begins with a computer design of a part. Machines then precisely remove material to turn the design into a real machined part. This cutting can be done from different angles using machines that have 3, 4, or 5 moving parts, known as axes.
At Futai, we have our own main CNC machine shop and a broad network of partner shops throughout China. Our facilities aren’t limited to just basic CNC machines. We also have grinders for smoothing surfaces, wire cutters for precise cuts, and EDM machines for detailed shapes. This variety allows us to tackle complex designs that produce unique CNC machined parts with specific requirements. Our skilled machinists work with exceptional accuracy, achieving tolerances as precise as 0.01mm. This level of detail is crucial for components that must fit perfectly into larger assemblies.
We also use automated production lines. These are setups where machines work together smoothly and quickly, which helps us produce large quantities faster and reduces the chance of errors. This efficiency means we can deliver quality machined parts quickly to meet our clients’ needs, keeping projects on schedule.
700+
Sets of Machine
120+
Countries Shipped
20,000+
Customers Served
Specialist Industries
Futai’s CNC machining services cater to a wide range of industries, from automotive to aerospace, ensuring that every sector’s unique requirements are met with precision.

Aerospace

Automotive

Automation

Medical Devices

Robotics

Consumer Products
Why Choose Us
Parts

Our team of experienced engineers utilizes the latest metal bending technology and rigorous quality control measures to ensure that every bent metal part meets the most exacting standards.
Lead Time

Our CNC bending equipment, coupled with streamlined workflows, allows us to turn around your custom bent parts in record time.
Support

Our experts guide you through the best choices for your project, from selecting materials to choosing bending methods, making sure you get optimal results every time.
FAQs
CNC machining has a wide range of applications across industries.
- In the automotive and aerospace sectors, it is used to fabricate precise engine components, structural parts, and other intricate elements.
- The medical industry leverages CNC for manufacturing devices, implants, and surgical instruments.
- CNC is also crucial in electronics, enabling the production of electronic housings, circuit boards, and connectors.
- Machine tool makers rely on CNC to create complex molds, dies, and machine components. Additionally,
- CNC is valuable for general custom part production, prototyping, woodworking, and more, allowing for consistent quality and high precision.
Advantages of CNC Machining
- Precision and Repeatability: CNC machining ensures high precision and consistent replication of parts, crucial for complex designs with tight tolerances.
- Reduced Human Error: The automated nature of CNC machining minimizes human error, enhancing the overall quality of production.
- Efficiency and Speed: Automation allows for faster production cycles, enabling quicker turnaround times than manual processes.
- Material Flexibility: CNC machines can work with a diverse range of materials, including metals, plastics, and composites, offering versatility across various applications.
- Software Integration: Advanced CNC software supports quick design changes and updates, facilitating rapid prototyping and easy customization.
- Cost-Effective for Large Runs: While setup costs are higher, per-unit costs decrease significantly with larger production volumes, making it cost-effective for mass production.
Disadvantages of CNC Machining
- High Initial Costs: CNC machinery and its maintenance represent significant investments, making initial setup expensive, especially for small-scale operations.
- Skill Requirements: Operating CNC machines requires highly skilled personnel, which can increase training costs and limit accessibility.
- Less Cost-Effective for Small Runs: Due to setup and programming time, CNC machining may not be economical for producing small quantities of parts.
- Material Waste: CNC machining often involves subtractive processes, leading to more material waste compared to additive manufacturing.
- Limited to Material Hardness: Extremely hard materials can wear out CNC tools quickly, potentially increasing operational costs and downtime.
Manufacturing Process: 3D printing is an additive process, building parts layer by layer from materials like plastic or metal. In contrast, CNC machining is subtractive, cutting away material from a solid block to shape the final product.
Material Efficiency: 3D printing minimizes waste by using only the material needed to form the part, whereas CNC machining can produce more waste due to its subtractive nature.
Speed and Cost: For small batches and complex geometries, 3D printing can be faster and more cost-effective. CNC machining is preferable for larger volumes and materials requiring high precision and strength.
Surface Finish and Tolerances: CNC machining typically achieves better surface finishes and tighter tolerances compared to 3D printing.
CNC Machining Resources

Metals
Metals such as aluminum, stainless steel, andbrass are known for their durability, highstrength, and excellent corrosion resistance.These properties make them ideal for bothstructural applications and detailed aestheticpieces.
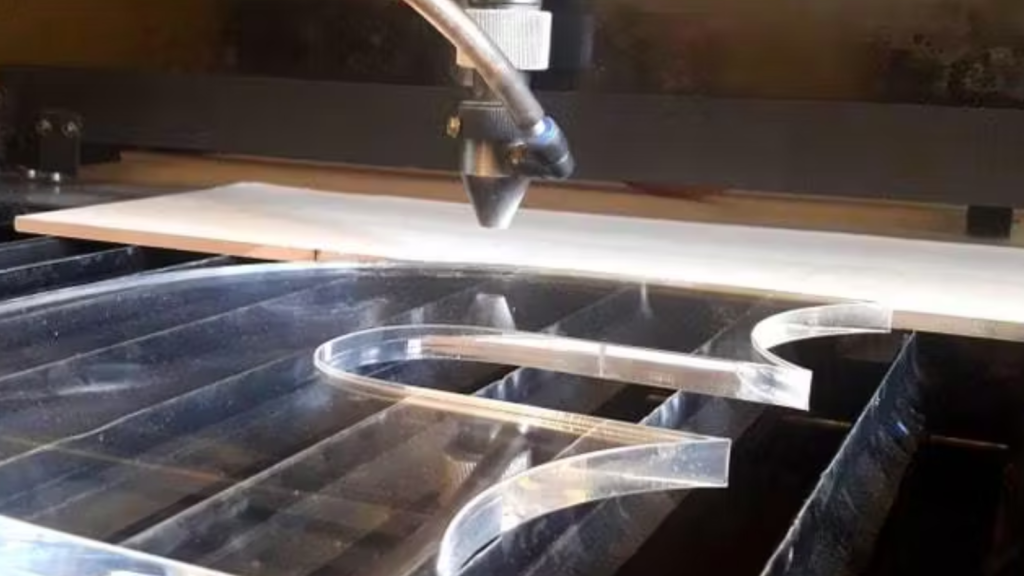
Plastics
Plastics like acrylic and polycarbonate arecelebrated for their lightweight, impactresistance, and clarity.These materials offergreat versatility, allowing for a wide range ofapplications from industrial components tovisually appealing decorative items.

Woods
Wood varieties such as pine, oak, and mapleare chosen for their natural grain patterns.workability, and strength. Each type provides aunique aesthetic and can be used for bothstructural purposes and intricate decorativeworks.