
Custom CNC Precision Machining
Get high quality precision CNC machined parts. Tolerances down to 0.01mm. Machined parts as fast as 1 day.
• Various rapid prototyping services
• Abundant materials & finishes
• 24/7 engineering support
What is Precision CNC Machining

Precision machining uses advanced CNC technology to create highly accurate parts needed in fields like aerospace, medical devices, and electronics. This process ensures every component meets exact specifications for size, shape, and function. CNC precision machining is essential for producing detailed and complex designs that regular machining can’t achieve. It allows for consistent production of high-quality precision machined parts and components, such as gears, brackets, and enclosures.
With Futai precision CNC services, industries can achieve tight tolerances and high precision, ensuring that each part functions perfectly in its specific application. These capabilities make it possible to manufacture parts that fit precisely within sophisticated machinery and devices, ensuring reliability and efficiency. Whether it’s small-scale prototypes or large-volume production, we deliver durable and dependable components.
Our Precision Machining Services
Wire EDM Service
Capability | Details/Specifications |
Material Compatibility | Stainless Steel, Titanium, Aluminum, Tool Steel, Copper |
Tolerance | ± 0.0001 inches (0.0025 mm) or better (based on material and thickness) |
Maximum Workpiece Size | Length: 16 inches (400 mm) Width: 12 inches (300 mm) Height: 8 inches (200 mm) |
Cutting Speed | Up to 300 mm2/min (specific to material and thickness) |
Surface Finish | As fine as Ra 0.2 µm |
Maximum Cutting Thickness | Up to 12 inches (300 mm) – varies based on material |
Wire Diameter Range | 0.004 inches (0.1 mm) to 0.012 inches (0.3 mm) |
Mirror EDM Service
Mirror EDM delivers mirror-reflective, high-precision parts. Capable of producing intricate shapes with tight tolerances, it excels on hard materials where conventional tools falter. Catering to industries from aerospace to electronics, our Mirror EDM ensures unparalleled precision, capturing intricate contours and complex geometries consistently.
Capability | Details/Specifications |
Material Compatibility | Stainless Steel, Titanium, Aluminum, Tool Steel, Copper |
Surface Finish | Achievable down to Ra 0.05 µm or better (based on material and process parameters) |
Tolerance | ± 0.00005 inches (0.0013 mm) or better (depending on material and thickness) |
Maximum Workpiece Size | Length: 16 inches (400 mm) Width: 12 inches (300 mm) Height: 8 inches (200 mm) |
Maximum Cutting Thickness | Up to 10 inches (250 mm) – varies based on material |
Grinding Service
Capability | Details/Specifications |
Material Compatibility | Stainless Steel, Aluminum, Tool Steel, Copper, Ceramics, Carbides |
Grinding Methods | Surface Grinding, Cylindrical Grinding, Centerless Grinding, Internal Grinding |
Tolerance | ± 0.0001 inches (0.0025 mm) or better (specific to material and grinding method) |
Maximum Workpiece Size | Length: 24 inches (600 mm) Width: 10 inches (250 mm) Diameter: 8 inches (200 mm) for cylindrical grinding |
Surface Finish | Achievable down to Ra 0.1 µm or better (based on material and grinding method) |

CNC Turning Service
Futai’s advanced CNC turning delivers unmatched accuracy and repeatability for machine parts and prototypes. Our diverse turning centers cater to varied applications, ensuring consistent precision across batches. With reduced errors, we offer quicker production without sacrificing quality. Rely on our technicians and top-grade CNC machines for exceptional component craftsmanship.
Capability | Details/Specifications |
Material Compatibility | Stainless Steel, Aluminum, Tool Steel, Copper, Brass, Titanium, Plastics |
Turning Operations | External & Internal Turning, Facing, Taper Turning, Boring, Drilling, Threading |
Tolerance | ± 0.0005 inches (0.0127 mm) or better (specific to material and operation) |
Maximum Workpiece Diameter | 20 inches (508 mm) or specific to machine capability |
Maximum Workpiece Length | 60 inches (1524 mm) or specific to machine capability |
Axis | 2-axis, 3-axis, multi-axis turning capability |
Bar Feeding Diameter | Up to 3 inches (76 mm) or machine-specific |
CNC Milling Service
Capability | Details/Specifications |
Material Compatibility | Stainless Steel, Aluminum, Tool Steel, Copper, Brass, Titanium, Plastics |
Milling Operations | Face Milling, Profile Milling, Pocket Milling, Complex Surface Milling, Drilling, Boring |
Tolerance | ± 0.0005 inches (0.0127 mm) or better (specific to material and operation) |
Maximum Workpiece Size | X: 40 inches (1016 mm) Y: 20 inches (508 mm) Z: 25 inches (635 mm) or specific to machine capacity |
Axis | 2-axis, 3-axis, multi-axis turning capability |
Bar Feeding Diameter | Up to 3 inches (76 mm) or machine-specific |

Futai Precision Machining Solutions
PROTOTYPING
Rapid Prototyping
Leverage our robust manufacturing capabilities for swift, high-quality prototype delivery. Using the latest technology, we ensure rapid, accurate production, expediting your path from testing to market.
Capability: 20-500
Lead Time: 10 business days
PRODUCTION
Low and High-Volume Production
Futai is equipped to handle large-scale production orders. This means that they can efficiently produce large quantities of precision machined parts without compromising on quality or precision.
Capacity: 1000+
Lead Time: 15 business days
Precision CNC Machining Tolerances
As an ISO 9001 certified company, we machine CNC turning lathe parts to meet tight tolerance requirements. Based on your design, our CNC lattes can reach tolerances of up to ±0.005”. Our standard tolerances for CNC milled metals is ISO 2768-m and ISO 2768-c for plastics.
Description
Maximum Part Size
Typically up to 500 mm in diameter and 1500 mm in length, though larger sizes can be accommodated with specific equipment.
Minimum Part Size
As small as 1 mm in diameter, depending on the material and machining setup.
Materials & Surface Finishes
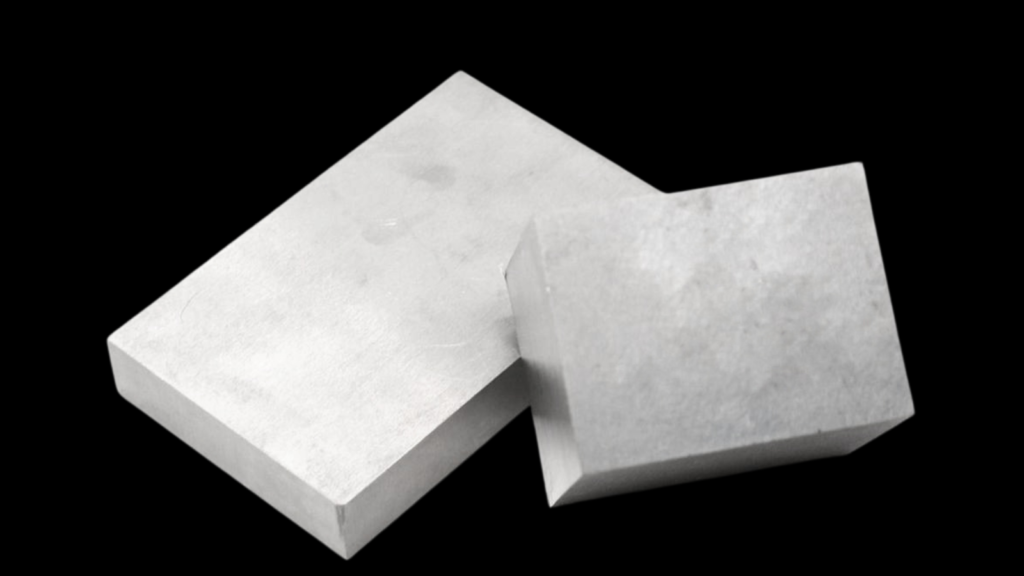
Metals
We provide a wide range of materials, including metals, plastics, and composites.

Surface Finish
We offer superior surface finishes that enhance part durability and aesthetics for applications requiring smooth or textured surfaces.
Advantages of Precision Machining
Precision machining offers significant benefits by producing parts with exceptional accuracy.
- High Accuracy: Precision machining tools can produce parts with extremely tight tolerances, ensuring that each piece meets exact specifications. This is crucial for applications requiring intricate details, such as in aerospace and medical devices.
- Consistency: This method offers unmatched consistency in production. Even over large volumes, each part remains identical, reducing the risk of errors and defects in the final product.
- Material Versatility: Precision machining can handle a wide range of materials, from metals to plastics and composites. This flexibility allows manufacturers to choose the ideal material for specific properties like strength, weight, or resistance.
- Complex Geometries: With advanced CNC machines, manufacturers can create complex shapes that would be difficult or impossible to achieve through manual processes. This capability is vital for developing innovative products and components.
- Reduced Waste: Since precision machining is so accurate, it minimizes material wastage. This efficiency not only saves on raw materials but also reduces the overall environmental impact of manufacturing.
- Speed: Modern precision machining techniques are highly automated, leading to faster production times compared to traditional methods. This speed enables quicker turnaround times for projects, keeping pace with market demands.
Applications of Precision Machining
Precision machining is integral in creating various specialized parts across multiple sectors:
- Engine Components: Essential for engines in both the automotive and aerospace industries, such as pistons and crankshafts, which require exact dimensions for optimal performance.
- Electronics Parts: Critical in producing components like connectors and pins in electronic devices, where precise measurements are necessary for functionality and compact assembly.
- Medical Implants: Used to manufacture surgical implants, including hip and knee replacements, where precise tolerances and smooth finishes are crucial for compatibility with human tissue.
- Aerospace Fasteners: Involves creating high-strength bolts and screws that must endure extreme environmental conditions in aerospace applications.
- Tool and Die Making: Focuses on crafting molds and dies that are fundamental in other manufacturing processes, ensuring the production of consistent and quality parts in mass production settings.
FAQs
Precision machining is necessary when your project requires components with extremely tight tolerances, intricate designs, or complex geometries that standard machining cannot achieve. This method is essential in industries where precision is critical, such as aerospace, medical devices, and electronics. If your parts need to perform under high stress, withstand extreme conditions, or fit into precise assemblies, choosing precision machining ensures the reliability and functionality of your products.
Yes, precision machining is specifically designed to provide tight tolerances. This technique can achieve tolerances as narrow as +/- 0.0005 inches, which is essential for creating highly accurate and consistent parts. The ability to maintain such precise measurements is crucial in applications where even the smallest deviation can lead to significant issues, such as in aerospace components or medical devices. Advanced CNC machines, which are commonly used in precision machining, are capable of producing parts with these strict specifications reliably.
To get a quote for a CNC precision machining project, you should prepare detailed information about your part or assembly, including CAD drawings, material specifications, and quantity needed. You will also need to specify the tolerances required and any additional post-processing like finishing or heat treating. With this information, go to Futai online platform where you can upload your design files and receive a pricing estimate quickly.