
Custom Online CNC Turning Services
Custom CNC turning services with fast lead times and competitive pricing from rapid prototyping to production runs. 0.02 mm tight tolerance. Lead time as fast as 1 day.
• Various rapid prototyping services
• Abundant materials & finishes
• 24/7 engineering support
Why Choose Us
With Futai CNC milling service, you’re investing in more than just machinery. You get the promise of impeccable precision, adherence to tight schedules, and the support of seasoned professionals.
Parts

Experience unparalleled precision in each undertaking. Our advanced milling processes ensure components adhere to tight tolerances, as tight as ±0.01mm, resulting in seamless assembly and operational excellence.
Lead Time

Accelerate your manufacturing cycle. Futai domestic workshops and state-of-the-art machinery guarantee fast turnaround times, helping businesses maintain momentum and meet critical deadlines.
Support

No matter you whenever and whereever, navigate your CNC milling projects with confidence. Our seasoned specialists offer insightful guidance at every step, maximizing design optimization and output quality.
CNC Turning With Futai
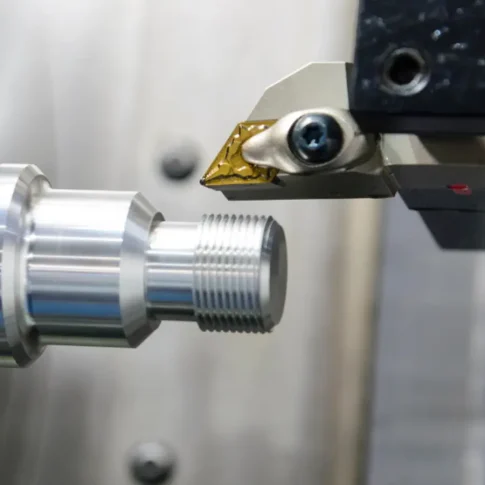
Take advantage of the on-demand CNC turning service and get reliable metal and plastic turned parts for your unique projects. With advanced technologies and expert technicians, RapidDirect produces high-quality custom prototypes and end-use production parts. Our CNC turning capabilities allow us to deliver turned parts with high accuracy, regardless of the complexity. You will get durable parts from flats to radial and axial holes, slots, and grooves as fast as one day.
Our precision CNC turning lathes provide low-cost parts for simple and complex cylindrical geometries. We also use Live tooling to create precise, complex geometries for features like axial and radial holes, grooves, slots, and flats. Full automation of these versatile machines allows us to produce hundreds of similar dimensions easier, faster, and cost-effectively.
Futai CNC Machining Solutions
PROTOTYPING
Rapid Prototyping
Accelerate product development with our rapid machining services. We offer fast turnaround times and specialize in quick production of high-quality prototypes and mold tooling, aiding your design verification process.
PRODUCTION
Low and High-Volume Production
Whether you need small batches or large-scale production, we can offer you both. With stringent tolerance controls and comprehensive capabilities, we adapt to your volume requirements without compromising on quality.
CNC Turning Materials
Our CNC turning processes are compatible with a wide range of materials, including machine-grade metals and plastics. Depending on your applications, we can create precise rapid prototypes and low-volume production from various superior-quality materials. Check out some of the common materials for your CNC turning projects.
![]() | Aluminum is lightweight yet strong, with excellent machinability and corrosion resistance. Ideal for aerospace and automotive parts. Alloys |
![]() | Copper is known for its superior electrical conductivity and thermal properties, making it perfect for electrical components and heat exchangers. Alloys |
![]() |
Brass is durable and has a low friction coefficient, which makes it suitable for fittings, tools, and musical instruments that require precision. Alloys Brass C27400 Brass C28000 Brass C36000 |
![]() |
Bronze is highly resistant to corrosion and metal fatigue, favored for bearings, bushings, and marine hardware.
Brass C36000Alloys Tin Bronze |
![]() |
Steel is an alloy with high tensile strength and durability, commonly used in construction and automotive industries for its robustness. Alloys Steel 1018, 1020, 1025, 1045, 1215, 4130, 4140, 4340, 5140, A36 Die steel Alloy steel Chisel tool steel Spring steel High speed steel Cold rolled steel Bearing steel SPCC |
![]() |
Stainless steel is renowned for its corrosion resistance, making it a prime choice for medical devices and food processing equipment. Alloys Stainless Steel SUS201 Stainless Steel SUS303 Stainless Steel SUS 304 Stainless Steel SUS316 Stainless Steel SUS316L Stainless Steel SUS420 Stainless Steel SUS430 Stainless Steel SUS431 Stainless Steel SUS440C Stainless Steel SUS630/17-4PH Stainless Steel AISI 304 |
![]() |
Magnesium is the lightest structural metal, offering high strength-to-weight ratios, perfect for automotive and aerospace applications where weight is critical.
Alloys Magnesium Alloy AZ31B Magnesium Alloy AZ91D |
![]() |
Titanium boasts the highest strength-to-density ratio among metals, highly resistant to corrosion and fatigue, ideal for aerospace, medical, and marine applications. Alloys Titanium Alloy TA1 Titanium Alloy TA2 Titanium Alloy TC4/Ti-6Al 4V |
CNC Turning Surface Finishes
With a wide selection of surface finishes, Futai can help improve the surface qualities of your products. Surface finishes applied to your CNC turned parts aim at improving their appearance, surface hardness and roughness, chemical and corrosion resistance, etc. They also help hide any visible tool marks from areas cut with live tooling. Here are some of your top choices.
As Machined

As machined finish leaves thesurface straight from the CNCmachine, providing a cost-effective option with toolmarks.
Anodizing
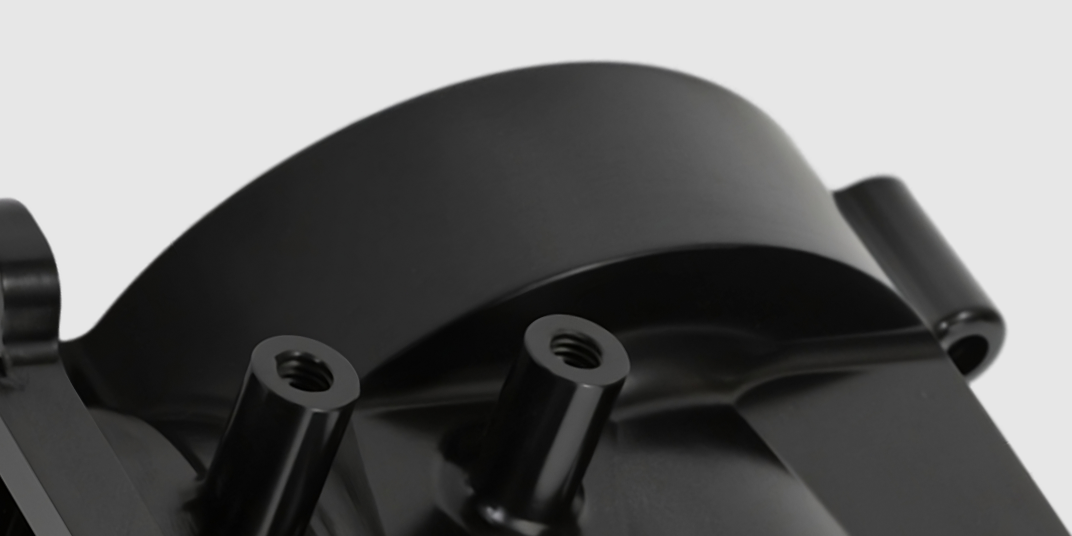
Anodizing increases corrosion resistance and wearproperties, while allowing forcolor dyeing, ideal for aluminumparts.
Polishing
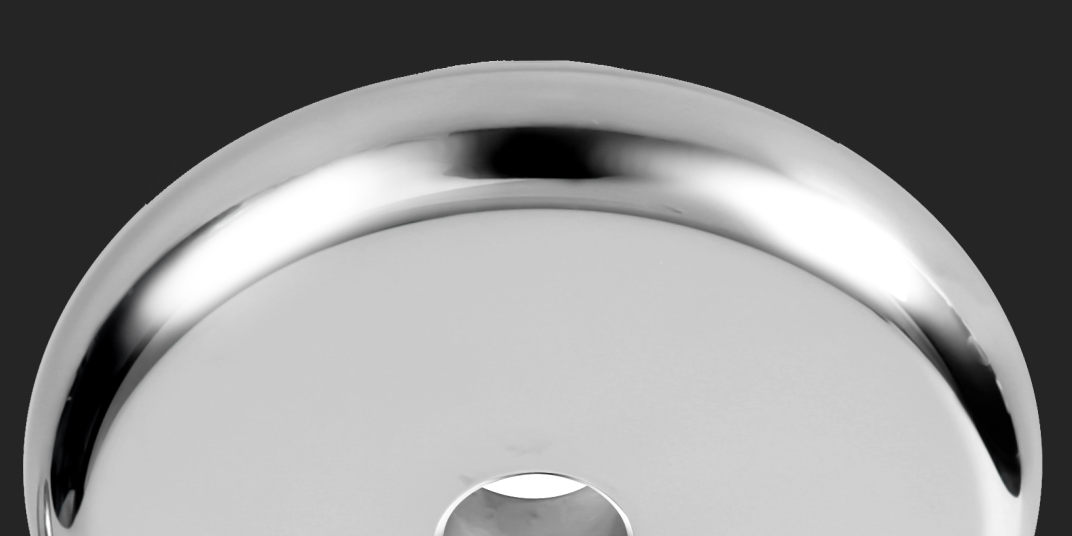
Polishing achieves a high glossfinish, reducing surfaceroughness and enhancing theaesthetic appeal of metals.
Sand Blasting
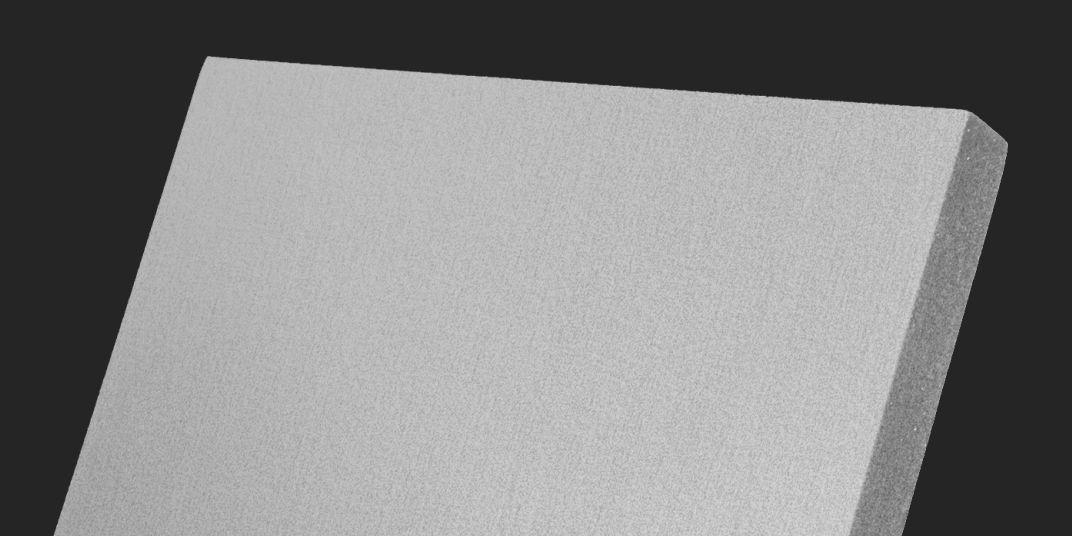
Sand blasting uses pressurizedsand or other media to cleanand texture the surface.creating a uniform,matte finish.
Tumbling

Tumbling smooths and polishes small parts by friction andabrasion in a barrel, offering aconsistent but slightly texturedfinish.
Electropolish
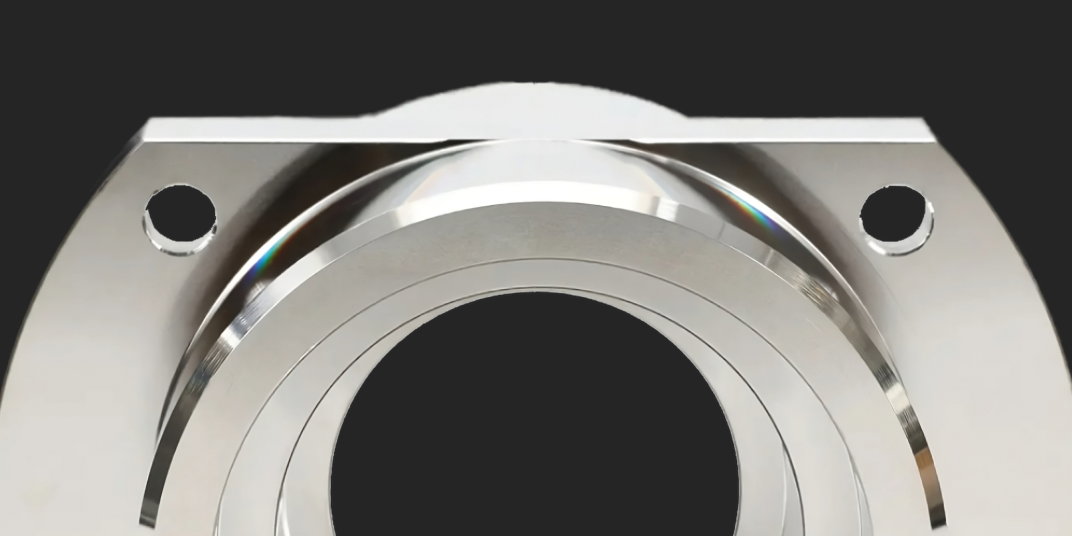
Electropolish is a chemicalprocess that smooths andbrightens surfaces whileimproving corrosion resistance.
Alodine

Alodine coating providescorrosion protection andimproves paint adhesion,mainly used on aluminumsurfaces.
Heat Treatment
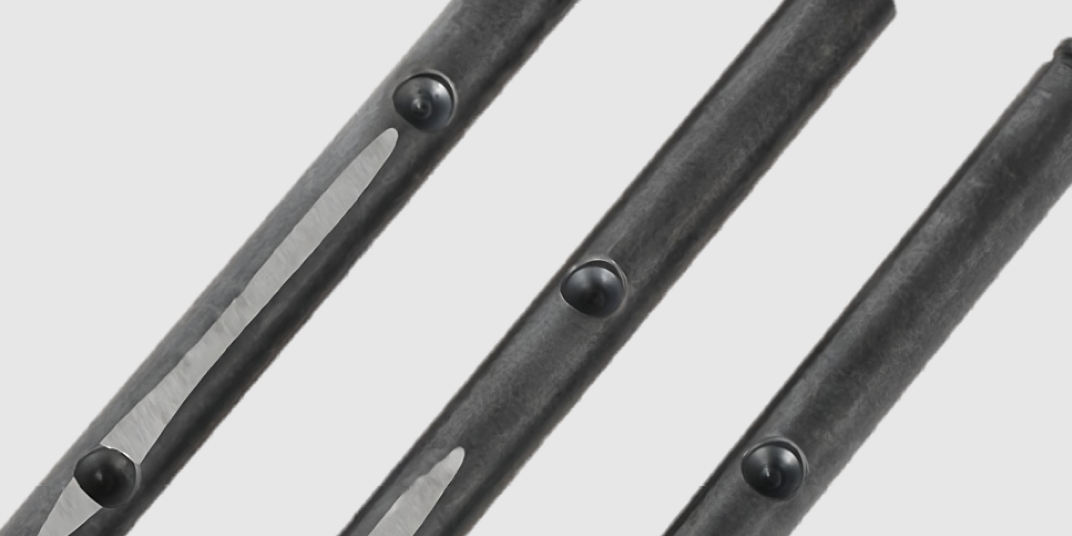
Heat treatment alters themechanical properties of metalto increase its hardness,strength, or ductility.
Brushed Finish

A brushed finish creates aunidirectional satin texture,reducing the visibility of marksand scratches on the surface.
Powder Coating
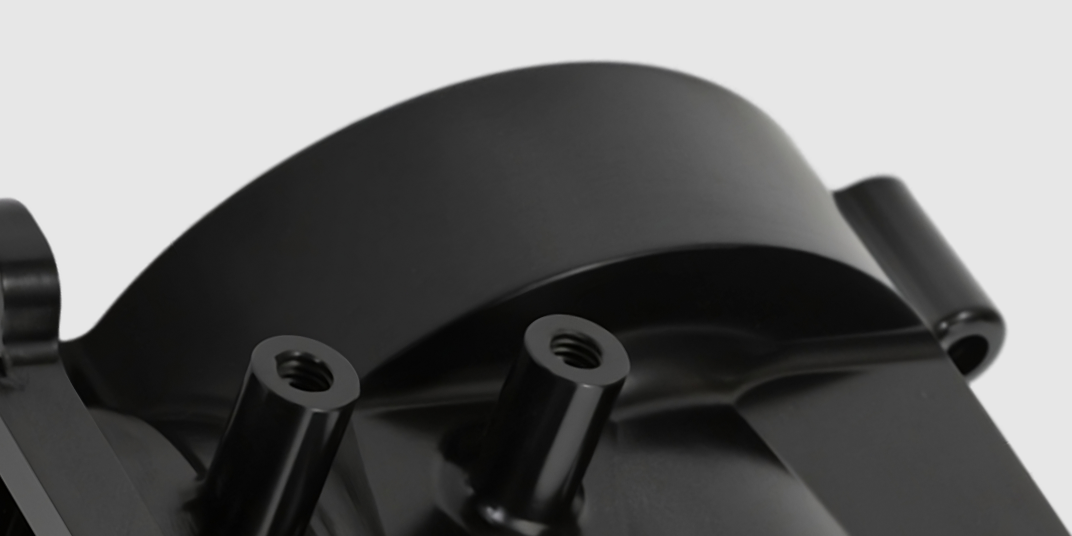
Powder coating applies a thick,wear-resistant layer withexcellent color and textureoptions, suitable for a variety ofsurfaces.
Electroplating

Electroplating bonds a thinmetal layer onto parts,improving wear resistance,corrosion resistance,andsurface conductivity.
Black Oxidize
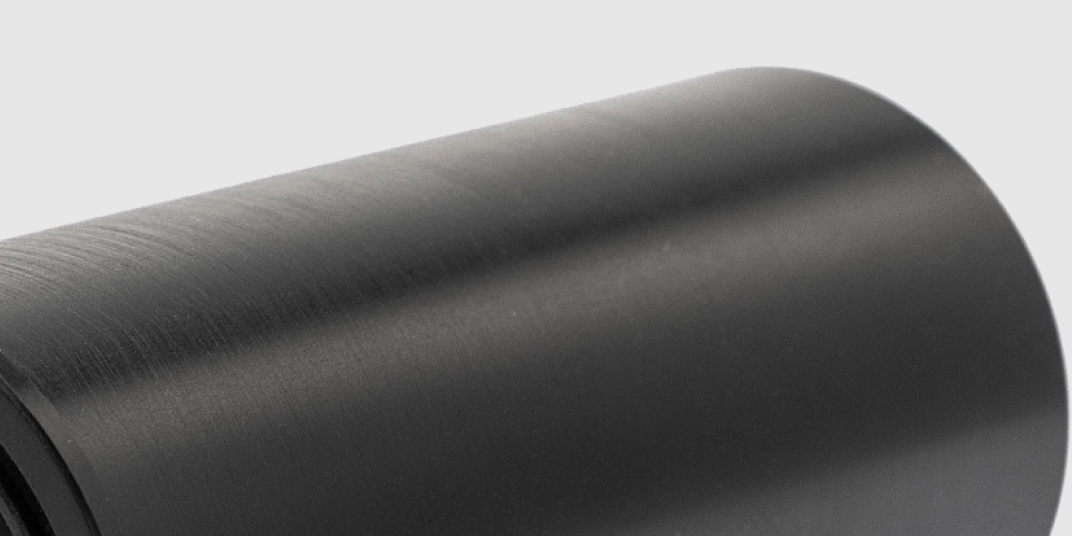
Black oxidize is a conversioncoating for ferrous metals thatimproves corrosion resistanceand minimizes light reflection.
Tolerances for CNC Turning
As an ISO 9001 certified company, we machine CNC turning lathe parts to meet tight tolerance requirements. Based on your design, our CNC lattes can reach tolerances of up to ±0.005”. Our standard tolerances for CNC milled metals is ISO 2768-m and ISO 2768-c for plastics.
Description
Maximum Part Size
Typically up to 500 mm in diameter and 1500 mm in length, though larger sizes can be accommodated with specific equipment.
Minimum Part Size
As small as 1 mm in diameter, depending on the material and machining setup.
CNC Turning Design Guidelines
Recommended Size
Radii
Internal radii should be at least 1/3 of the cavity depth. Use larger radii whenever possible.
Threads and Tapped Holes
Diameter Φ 1.5-5 mm, depth: 3 times the diameter.
Diameter Φ 5 mm or larger, depth: 4-6 times the diameter.
RapidDirect can produce threads of any specification and size as required by the customer.
How Does CNC Turning Work?
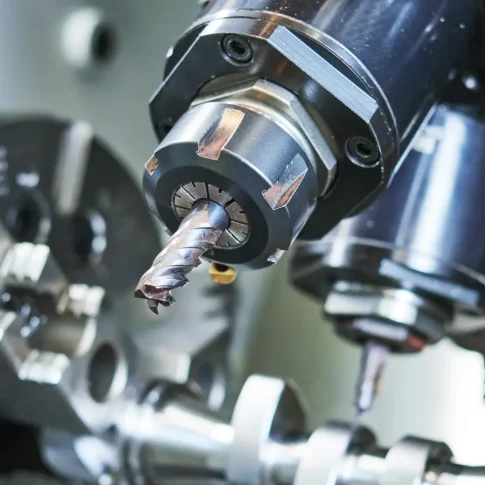
As the machine operates, the workpiece spins at high speeds while the cutting tools move along various axes to carve, cut, and shape the material based on the program’s specifications. Operations such as facing, threading, knurling, and drilling are performed during this stage. A coolant is often applied to prevent overheating and to wash away debris.
After machining, the part may undergo additional finishing processes like sanding or polishing. The final step involves a thorough inspection to ensure the part meets all the required dimensions and tolerances. This process allows for high precision and repeatability, making CNC turning ideal for producing complex parts efficiently.
Advantages of CNC Turning
CNC turning offers several distinct advantages that make it a preferred method for manufacturing precise cylindrical parts. Here are some of the key benefits:
- High Precision: CNC milling machines can produce parts with very tight tolerances, ensuring high accuracy and consistency in every piece.
- Complex Geometries: With the ability to move in multiple axes, CNC milling can create intricate and complex shapes that are difficult or impossible to achieve with manual machining.
- Efficiency: Automated operation allows for continuous production, reducing lead times and increasing productivity. Multiple parts can be produced with minimal downtime.
- Flexibility: CNC milling can work with a wide range of materials, including metals, plastics, and composites. This versatility makes it suitable for various applications.
- Repeatability: Once a design is programmed, the machine can reproduce identical parts over and over, ensuring uniformity and reducing the risk of human error.
- Cost-Effective: While the initial setup can be expensive, the efficiency and precision of CNC milling reduce overall production costs, especially for large quantities.
- Safety: CNC machines operate with minimal human intervention, reducing the risk of accidents and enhancing workplace safety.
Applications of CNC Turning
CNC turning is adept at producing a variety of precision components, often used in mechanisms where accuracy and fit are critical. Here’s an overview of some typical parts made through this process:
- Shafts are fundamental in various machines, serving as axes or pivots. Precision in diameter and surface finish is crucial for their interaction with other mechanical parts.
- Flanges connect pipes, pumps, or valves, requiring accurate machining to ensure a secure fit and avoid leaks.
- Bushings and Sleeves provide smooth surfaces for other parts to move against or through, necessitating exact internal diameters and smooth finishes.
- Pins are small but vital for aligning or holding components together, often needing precise dimensions to fit snugly into place.
- Knobs and Dials are user interface elements for machinery and electronic devices, where aesthetics and precise dimensions enhance usability.
- Wheels and Rollers are integral to systems like conveyors, where consistent shape and smoothness reduce friction and wear.
FAQs
CNC turning produces cylindrical and symmetrical parts around their axis. This process is typically used for manufacturing items like shafts, pins, rods, bushings, and pulleys. It’s also well-suited for creating external threads, internal boreholes, and even complex contours on cylindrical surfaces. The precision of CNC turning allows for tight tolerances and a smooth finish, making it ideal for parts that require exact fits and movements, commonly found in automotive, aerospace, and manufacturing machinery.
Yes, CNC turning is versatile enough to handle various materials, including plastics. Plastics commonly turned on CNC lathes include ABS, Polycarbonate, PTFE (Teflon), Nylon, and Acetal. Each material offers different properties; for instance, Nylon is known for its strength and friction resistance, while Acetal provides excellent machinability and dimensional stability. Turning plastics requires precise control of cutting speeds and tool selection to prevent melting or deformation, ensuring the production of high-quality, precise parts suitable for a range of applications.
CNC milling and CNC turning are both subtractive manufacturing processes, but they differ in how the material is removed.
In CNC milling, the workpiece is stationary, and the cutting tool moves across multiple axes to remove material and create the desired shape. This process is ideal for complex parts with various features such as slots, holes, and contours.
On the other hand, CNC turning involves rotating the workpiece while a stationary cutting tool removes material. This method is best suited for producing cylindrical parts, such as shafts, rings, and bolts. While milling can handle more complex geometries, turning is typically faster and more efficient for producing round parts.
CNC Turning Resources

Metals
Metals such as aluminum, stainless steel, andbrass are known for their durability, highstrength, and excellent corrosion resistance.These properties make them ideal for bothstructural applications and detailed aestheticpieces.
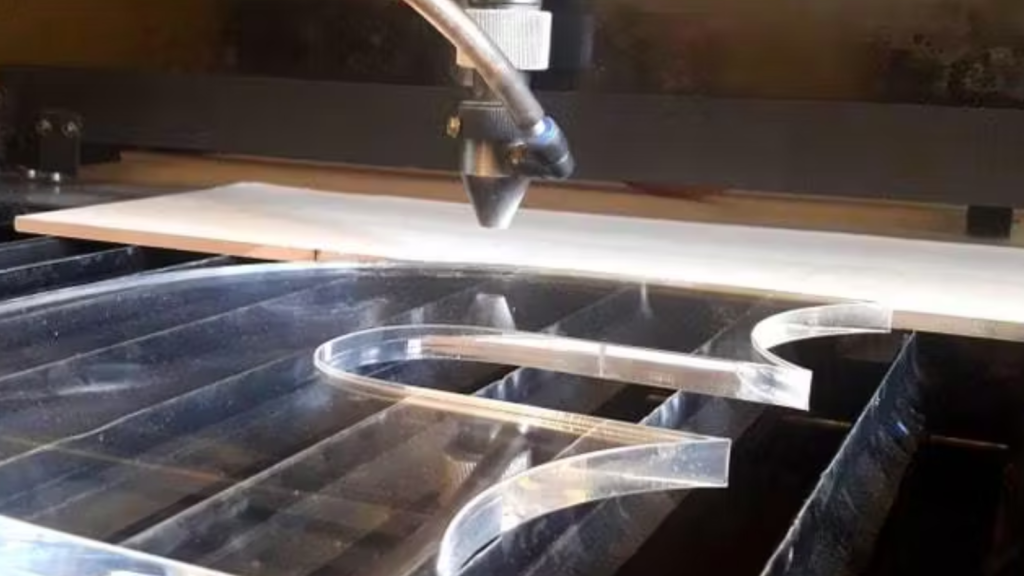
Plastics
Plastics like acrylic and polycarbonate arecelebrated for their lightweight, impactresistance, and clarity.These materials offergreat versatility, allowing for a wide range ofapplications from industrial components tovisually appealing decorative items.

Woods
Wood varieties such as pine, oak, and mapleare chosen for their natural grain patterns.workability, and strength. Each type provides aunique aesthetic and can be used for bothstructural purposes and intricate decorativeworks.